OUR Services
A comprehensive range of pre-treatment, coating and finishing services.
Blast Cleaning
At Mastercote we have two blast containers where we use chilled iron or steel grit to blast surfaces clean of scale, rust, old paint and other contaminates. In order for a coating system to work properly in the field it is essential that the surface is properly cleaned, and blasting is the most effective method on most substrates, particularly if the customer is concerned about longevity of the paint finish. Unless specified otherwise by our customers, we always blast clean to the International ISO-8501-1 standard SA 2 ½ – “Very Thorough Blast Cleaning”.
For coated items it is often necessary to use a pyrolysis oven to heat the metal to over 400 degrees prior to blast cleaning. This process causes the paint/powder coating to peel and greatly reduces the time taken to blast the items, thus saving the customer money. It is imperative that customers inform us of anything that might not withstand such temperatures before it arrives with us.
Anti-Corrosion Priming
We made the decision a few years ago to apply an anti-corrosion powder or wet primer to all products likely to either spend time outside or come into contact with contaminants that might affect the lifespan of the coating. Steel products are blast cleaned and are then coated once with an anti-corrosion powder or wet primer before being coated for a second time using the customer’s colour and finish of choice.
Hot Zinc Flame Spraying
Being used increasingly as an easier and cleaner alternative to hot-dipped galvanising, zinc offers excellent corrosion resistance in some of the harshest environments. Unlike galvanising there is no risk of heat distortion, and no need to fettle runs and sharp edges.
Before applying the zinc spray we blast clean the substrate to provide a roughened surface free of any oil or debris that could cause contamination. Molten zinc is then hand sprayed onto the surface of the substrate, generally to around 60-80 microns though thicker coats would be required for offshore work.
Once applied the zinc must be sealed or painted to give additional protection. For gates, railings and other items to be powder coated we always apply an anti-corrosion primer before adding the customer’s required colour coat which gives three layers of excellent corrosion resistance.
FAQ’s
When Are You Open?
Our office hours are 8am to 4:30pm Monday to Thursday and 8am to 2:30pm on Friday.
Deliveries and collections need to be made 30 minutes before our closing time and it is always advisable to call ahead. We do not open for business on weekends or bank holidays.
What is Powder Coating?
Powder coatings are a mixture of polymer resin systems, curatives, pigments, levelling agents, flow modifiers and other additives which are melt mixed, cooled and ground into a uniform powder similar to baking flour.
How is Powder Coating Applied?
Powder coatings are applied by a process called electrostatic spray deposition. The application method uses a spray gun which applies an electrostatic charge to the powder particles which are then attracted to the (grounded) metal substrate. After application the parts enter a curing oven where, with the addition of heat, the coating chemically reacts to produce long molecular chains resulting in high cross-link density.
How Durable is Powder Coating?
Powder coatings provide one of the longest-lasting and durable finishes available. Coatings are more resistant to chipping, scratching, fading and wearing than other types of coating and special high-durability powders can be sourced from suppliers to give customers extra peace of mind.
How Thick is Powder Coating?
Mastercote aims to apply a minimum of 80 microns (0.08mm) to goods to ensure good protection to the substrate.
How Environmentally Friendly is Powder Coating?
Powder coatings are now very friendly to the environment thanks to the removal of most of the volatile organic compounds (VOCs). Unlike most wet paints it also contains no solvents.
What Colours are Available?
Please see the RAL range of colours here: https://www.ralcolorchart.com/ . We also stock, or can source, a wide range of specialist colours including pearlescent, metallic, British Standard and super durable colours.
Do We Offer Chrome Plating?
No. We are very often asked this question but unfortunately it’s not something we currently offer and we haven’t yet been able to find a suitable powder coating that replicates the mirror finish of chromium.
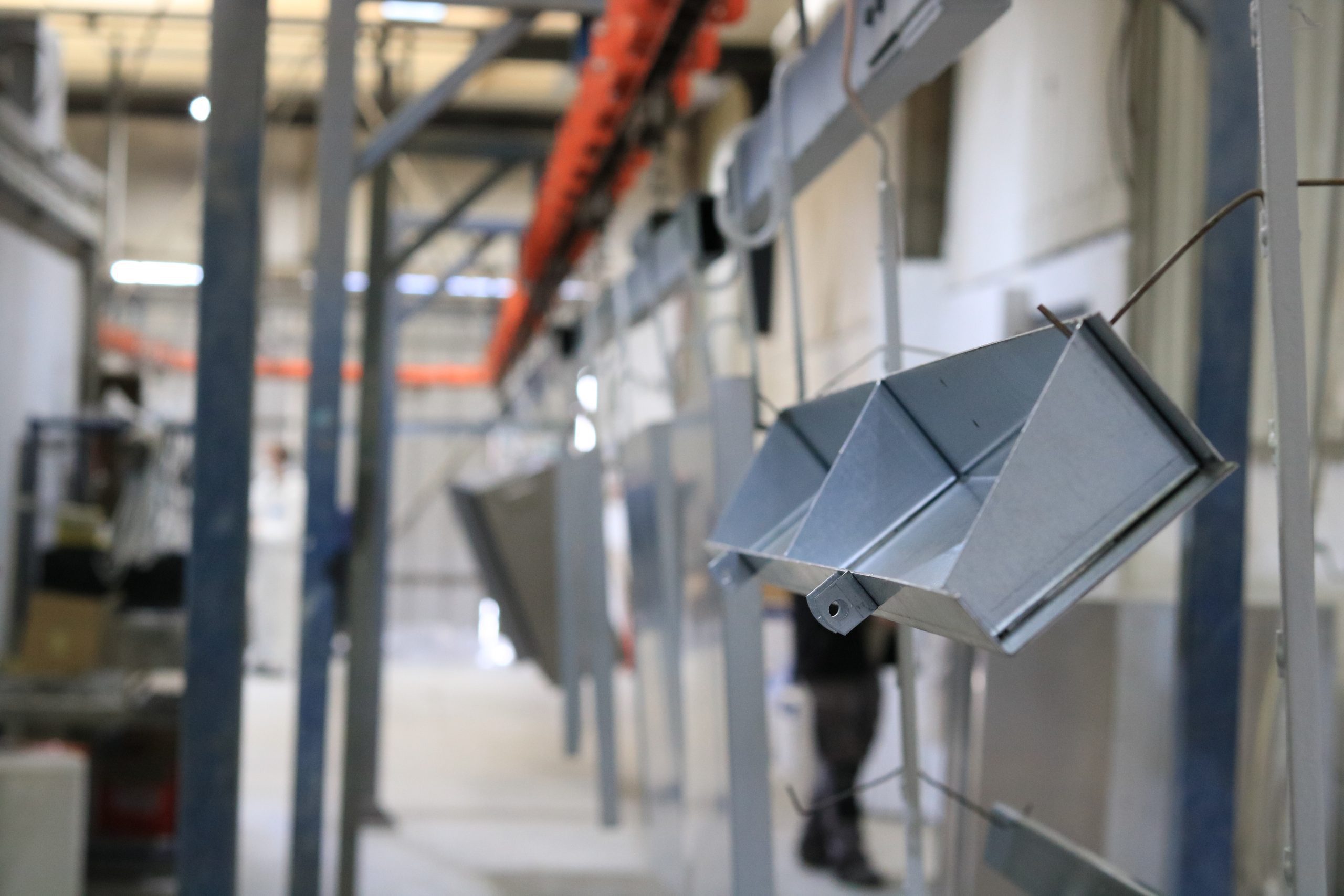
Non-Chromate Aluminium Pretreatment
Our six stage aluminium pretreatment system involves immersing the aluminium or alloy in 7.5 metre long baths of a variety of chemicals and rinses and produces an excellent base for coating, ensuring a hard-wearing, corrosion-free surface.
After being dipped in an acid etch cleaner to remove oils or any other contaminants from the surface, the aluminium is placed in three separate rinse tanks (two towns, one demineralised) before being immersed in the conversion coating. This forms a bond with the clean, etched aluminium and once it has been through a final demineralised rinse and dried in an oven it is ready to be coated, subject to the necessary QC checks.
Powder Coating
We only use the very best architectural grade powders and have 100s of colours in various gloss levels in stock. We have two on-line coating plants that can handle material up to 7.5 metres in length, and two box ovens that cater for wider, taller or heavier items.
Powder coatings are applied by a process called electrostatic spray deposition. The application method uses a spray gun which applies an electrostatic charge to the powder particles which are then attracted to the (grounded) metal substrate. After application the parts enter a curing oven where, with the addition of heat up to 200 Celsius, the coating chemically reacts – melting and adhering to the substrate. It is imperative that customers inform us of anything that might not withstand such temperatures before it arrives with us.
Wet Painting
We’re specialists in the coating of uPVC windows, doors, fascia’s, guttering and all other goods for the home improvements trade. With manufacturers generally supplying in a very limited choice of colours, and operating with a largely extended lead-time for anything bespoke, we are able to transform them with an almost unlimited choice of colours within 5-7 working days.
Many people are now choosing to keep the inside of their frames white whilst showing a more personalised colour to the outside world. This is something we’re experts at, using a range of high quality paints and masking tapes to give you the finish you desire.
We can also wet paint for the automotive, manufacturing and construction industries, with wheels, frames, tools, gates and railings regularly passing through our spray-bake unit.
FAQ’s
What Can’t You Powder Coat?
Anything that cannot be heated up to above 160-180 degrees. Rubber and plastic will not survive and must be removed, or you must choose to have the products wet coated.
What Is Wet Coating?
Wet coating is the application of a liquid paint to products that typically cannot be heated to temperatures required by powder coatings, or those that require specialist finishes that the powder coatings industry cannot yet achieve.
How is Wet Coating Applied
The majority of paints that we use are two pack products that are carefully mixed before being applied through a spray gun. The material to be coated will be free from contaminants, rust and debris and a selected prime coat may be applied before the decorative top coat, depending on customer requirements.
How Durable is Wet Coating
Typically not as durable as some powder coatings, though wet coating has been used for many years in the offshore industry and the preparation, pre-treatment, selection and application of paint products will produce a stable, long-lasting finish.
How Thick is Wet Coating
Typically thinner than powder coating – a coat of a two pack polyurethane to a PVCu window or electronic casing will add around 30 microns (0.03mm). However some specifications call for specialist paints and/or multiple coats adding up to over 300microns (0.3mm)
What Colours are Available?
An advantage wet coatings have over powder coatings is the almost limitless range of colours available. We offer a colour match service which has seen us wet coat customer goods to match their curtains, walls and even a packet of crisps!
How Long Is Your Turnaround?
At present our average turnaround time is around 5-7 working days, depending on what is required.
Can We Collect / Deliver?
We do not run our own vehicles but can arrange for a transport company to collect and deliver at an additional charge.
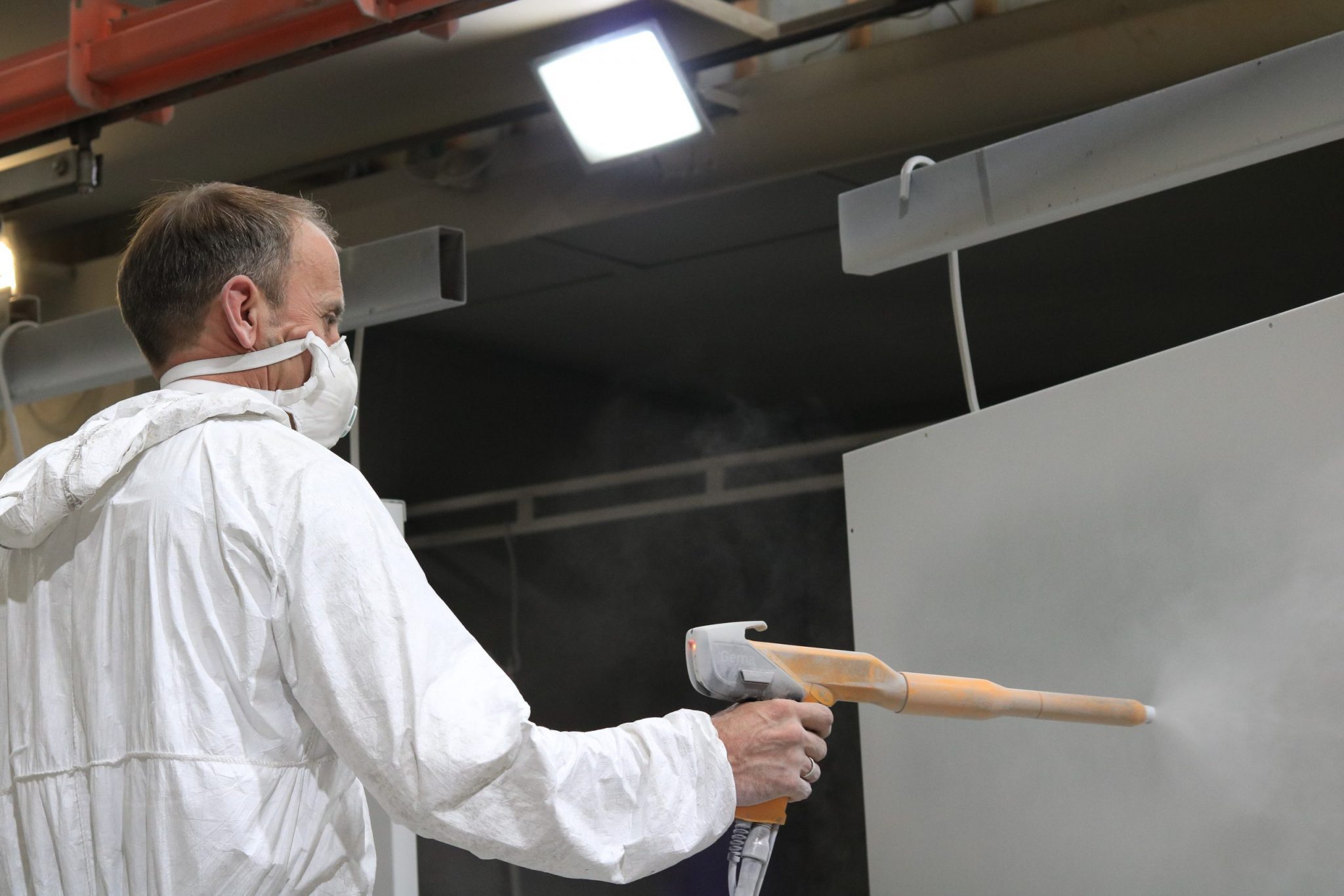
Address
52-54 Wendover Road
Rackheath Industrial Estate
Norwich
NR13 6LH
Contact
+44 (0)1603 720326
sales@mastercoteuk.co.uk